“Preventing Rust with Rust?What is Weathering Steel COR-TEN®︎?”~vol.2~
- Product
- COR-TEN
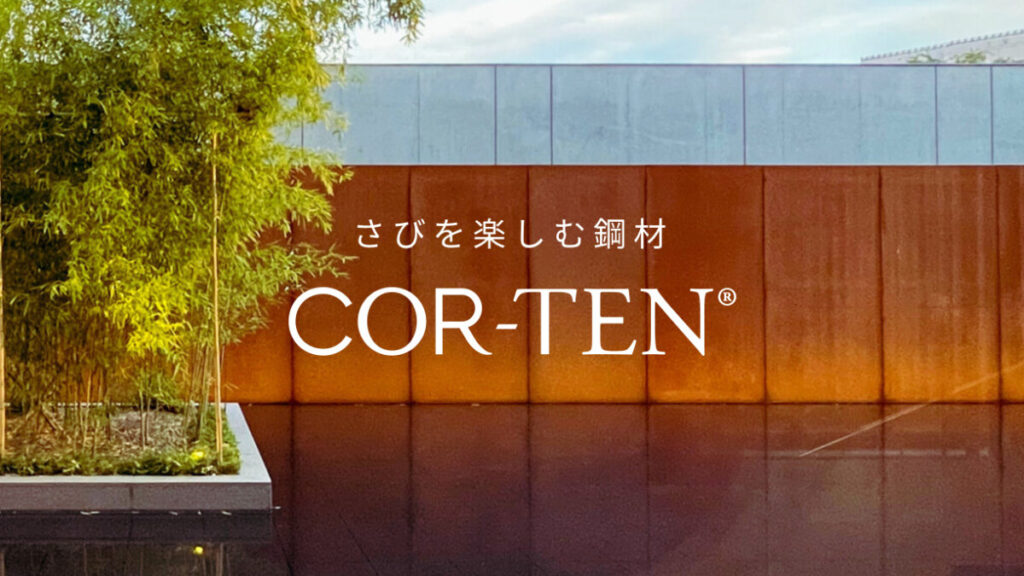
※)The content of this article reflects our opinion and does not guarantee completeness or accuracy. When purchasing or processing products, please consult with specialized professionals, including our company, and verify the material based on its intended purpose and application before use.
“Vol. 1 is available here ↓↓ !!”
In the previous volume (Vol. 1), we explained the overview of weathering steel COR-TEN®︎, including its rust color, usage with or without painting, and surface treatments. In this volume, we will discuss its specific applications, key considerations, standards, and welding techniques.
How is weathering steel COR-TEN®︎ steel used?
The basic usage methods for COR-TEN®︎ steel can be categorized into three types: uncoated, rust stabilization assistance treatment (which is also considered a type of uncoated usage since it is not painting), and painted. A simplified summary of these usage methods is shown in Table 1.
Whether painted or unpainted, considering the advantages of using weathering steel requires focusing on aesthetics and life cycle cost (LCC). Regarding LCC, while the initial construction cost may be slightly higher than painting regular steel, the reduced need for repeated repainting lowers maintenance expenses. As a result, the total cost over the lifespan of the structure becomes more economical.
Even if you purchase a cheaper product initially, repeated repairs can make it more expensive in the long run. Therefore, it may be preferable to choose a slightly more expensive option at the time of purchase if it requires lower maintenance costs.
However, one important consideration when using weathering steel is that if the environmental conditions are unsuitable—such as excessively high airborne salt levels—the protective rust layer may fail to form properly. In such cases, painting may become necessary after all.
For regions near coastlines, careful consideration is required before application. As a general guideline, in Japan, organizations such as the Civil Engineering Research Institute and the Steel Materials Club suggest that on the Pacific side, applicable areas are those more than 2 km away from the coastline, while on the Japan Sea side in the Hokuriku and Tohoku regions, the recommended distance is more than 20 km. However, if airborne salt levels are low, application may still be feasible outside these designated areas. Since airborne salt concentration varies depending on wind direction, terrain, and elevation, these factors must also be taken into account.
Nippon Steel has also developed technology to estimate the corrosion amount 100 years into the future(2). Additionally, although it is not marketed under the COR-TEN®︎ brand name, a nickel-based highly weather-resistant steel has been developed for environments with higher airborne salt levels.
(2) Kihira et al.: Study on the Corrosion Degradation Prediction Model for Weathering Steel. Journal of the Japan Society of Civil Engineers (2005), Issue 780, pp. 71-86.
Usage method | Benefit | Disadvantage | LCC |
Uncoated | Generally does not require additional maintenance (checking the condition of the rust is necessary). | Initial rust (yellow rust, streaking rust) occurs, and if airborne salt levels are high, protective rust may not form. | ★★★ |
Rust stabilization assistance treatment | No issues with initial rust. Over time, it transitions into protective rust. | Unevenness occurs when the coating is replaced by protective rust. | ★★ |
Coating | The repainting cycle is extended. | Initial costs are higher. | ★ |
Standards for COR-TEN®︎ steel
The standards for COR-TEN®︎ are established by USS.
As shown in Table 1, Nippon Steel has established a slightly modified version of the standard for the domestic market. While the composition that determines weather resistance is maintained, the mechanical properties have been slightly adjusted for domestic use.
Weathering steel containing phosphorus | General weathering steel (50 k) | General weathering steel (60 k) | |
USS standards | COR-TEN A | COR-TEN B | COR-TEN B-QT |
Equivalent standards of Nippon Steel.” | COR-TEN O | COR-TEN490@ | COR-TEN570 |
The most widely sold COR-TEN®︎ in Japan so far is COR-TEN O (Corten O), which contains a large amount of phosphorus (P) and emphasizes weather resistance. It corresponds to COR-TEN A under the USS standards.
COR-TEN A has a maximum plate thickness of 1/2 inch (12.7 mm), while COR-TEN O is listed in catalogs with a maximum thickness of up to 76 mm. However, it is typically used at 12 mm or, at most, up to 25 mm. Due to its high phosphorus (P) content, which can degrade the properties of welded areas, special care must be taken when welding COR-TEN O. I will write separately about welding weathering steel.
In addition to hot-rolled steel plates, including thick plates, COR-TEN O is also available as cold-rolled steel sheets, structural steel sections, and steel bars. Since they share the same weathering elements, they exhibit similar weather resistance.
In addition to COR-TEN O, there are COR-TEN 490 and COR-TEN 570, which also have general weather resistance. They primarily consist of hot-rolled steel plates, mainly thick plates. The difference between COR-TEN 490 and COR-TEN 570 lies only in strength and toughness levels, while their weather resistance remains the same.
Table 2 presents the chemical composition of each steel type, while Table 3 shows their mechanical properties.
COR-TEN O contains approximately 0.1% phosphorus (P), which is about one order of magnitude higher than that of general steel. With recent advancements in steelmaking technology, phosphorus levels have become extremely low, making its addition necessary. I have heard that an iron pillar in India has remained intact for over 1,500 years, supposedly due to India’s climate and the high phosphorus content in the iron of that era. If true, that would be fascinating.
In terms of mechanical properties, COR-TEN O and COR-TEN 490 fall into the 50-k class, while COR-TEN 570 belongs to the 60-k class. COR-TEN O and COR-TEN 490A do not have guaranteed toughness, but they do possess a certain level of toughness. Therefore, in thinner materials, the toughness of the base metal is unlikely to be a significant issue.
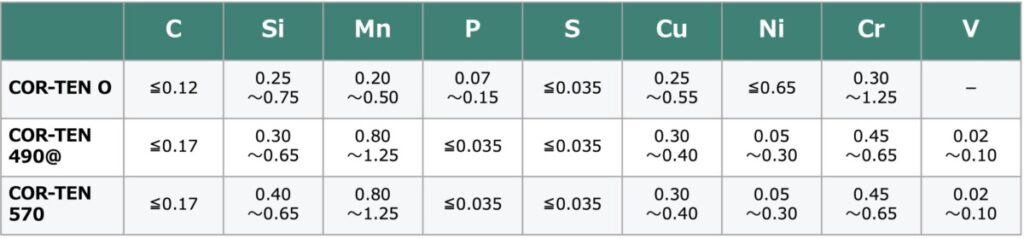
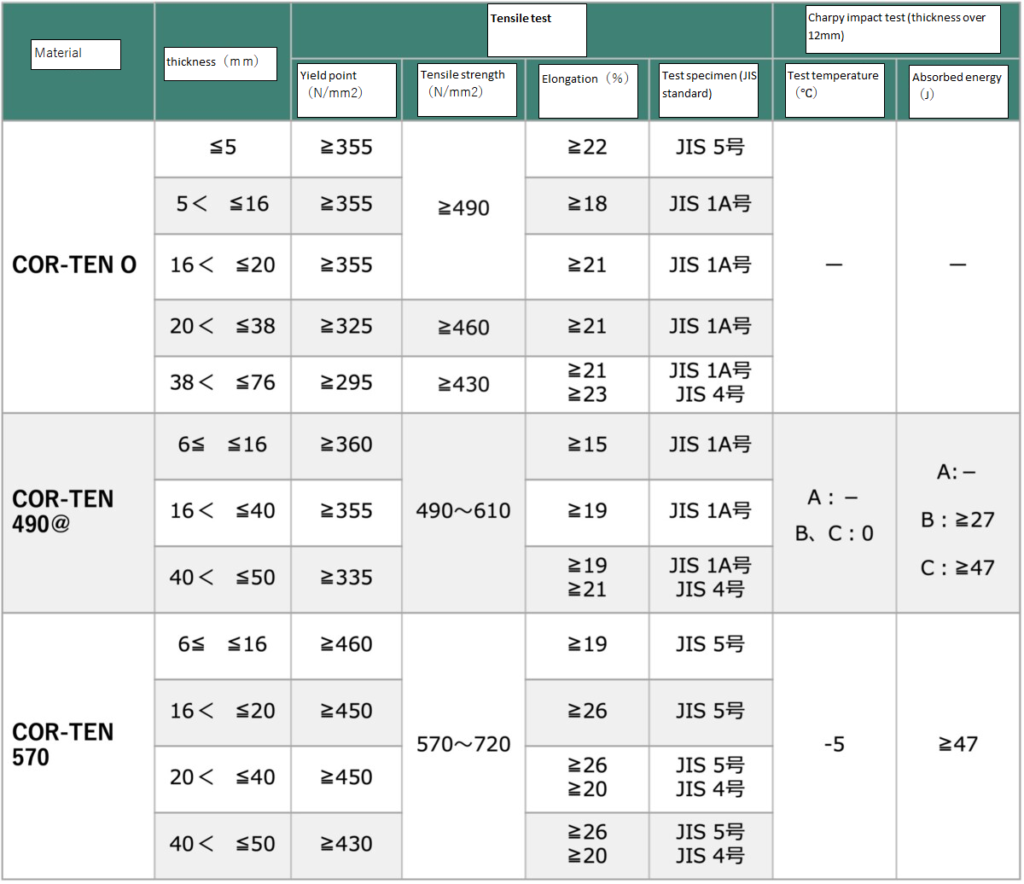
Welding of COR-TEN®︎ steel
COR-TEN®︎ steel requires dedicated welding materials. If the welded area does not have the same weather resistance as the base material, only the base material will form a protective rust layer, while the welded area will continue to corrode.
Table 4 presents a list of welding materials, which are sold by Nippon Steel Welding Industry Co., Ltd. Whether preheating is necessary for welding is somewhat ambiguous, but the welding material manufacturer recommends slight preheating for plate thicknesses exceeding 25 mm.
For COR-TEN O, the high phosphorus (P) content in the base material makes it unsuitable for welding. Matching the welding material to this composition can lead to high-temperature cracking in the welded area and a decrease in toughness.
When welding, it is recommended to use plates with a thickness of less than 13 mm. Welding should be performed with low current and low heat input to minimize penetration into the base material as much as possible. The welding material used will be repurposed from COR-TEN 490.
In that sense, the weather resistance of the welded area will be slightly lower than that of the base material, but it has never been an issue so far.
The manufacturer does not permit welding for plate thicknesses over 13 mm; however, there have been cases where such welding has been carried out and used in practice. As long as the welded area is not used as a load-bearing structural component and defects in the welds are properly inspected, it should not pose an issue. That said, using COR-TEN 490 might be the safer option.
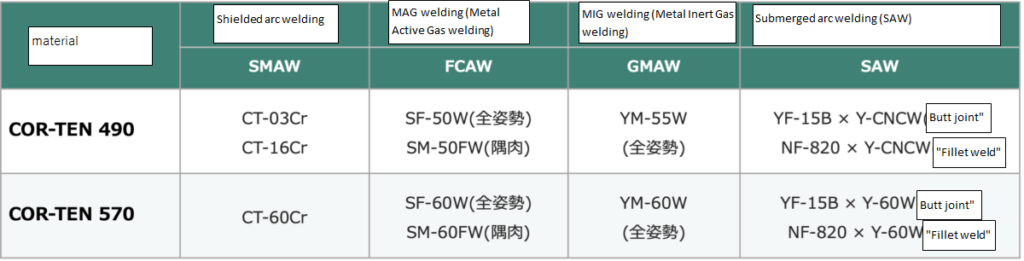
Alternative Uses of COR-TEN®︎ Steel Beyond Its Weather-Resistant Properties
As I have written so far, COR-TEN®︎ is primarily used as weather-resistant steel. However, COR-TEN O, in particular, has applications beyond this.
For example, in concrete mixers, COR-TEN®︎ steel is used not only for its corrosion resistance but also for its excellent wear resistance. Its strength, at around the 50-kilogram level, may also be a contributing factor. It is also used in coal freight cars. In garbage trucks, it appears to be effective in preventing corrosion caused by wastewater.
In conclusion
That concludes the explanation of COR-TEN®︎ steel. It is often requested as a sample; however, before it rusts, its appearance is no different from ordinary steel. Even in the early stages of rust formation, distinguishing its unique characteristics can be difficult.
Like whiskey, it takes years of aging for COR-TEN steel to develop its distinctive textured rust. Without seeing the actual material, it may be difficult to visualize the rust formation. I hope that by referring to Nippon Steel’s catalog¹, more people will become fans of COR-TEN®︎.
Here is our special website (Currently, it is only available in Japanese—sorry about that!
“Our company is…”
We are a specialized trading company based in Japan, dealing in high-tensile steel and other special steels.
Please feel free to contact us.
Feel free to email us.
↓↓↓
info@kumagai-steel.co.jp